Bancroft Engineering stands at the forefront of manufacturing innovation, specializing in designing and producing cutting-edge automated welding equipment. Laser Beam Welding (LBW), a signature technology, is a testament to this. LBW uses laser beams to achieve...
Welding Systems
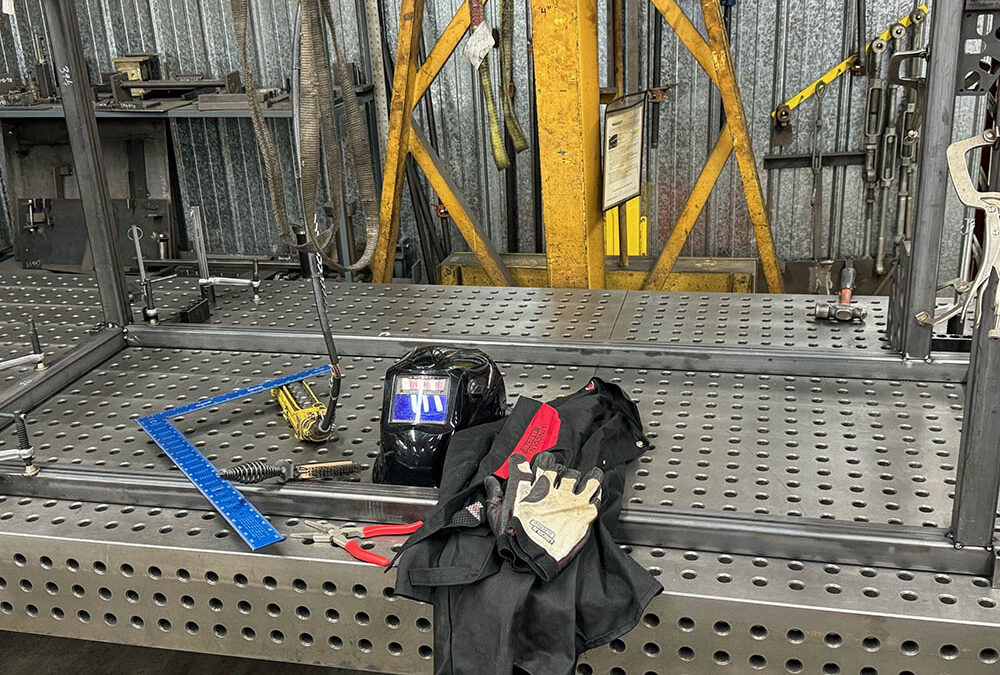
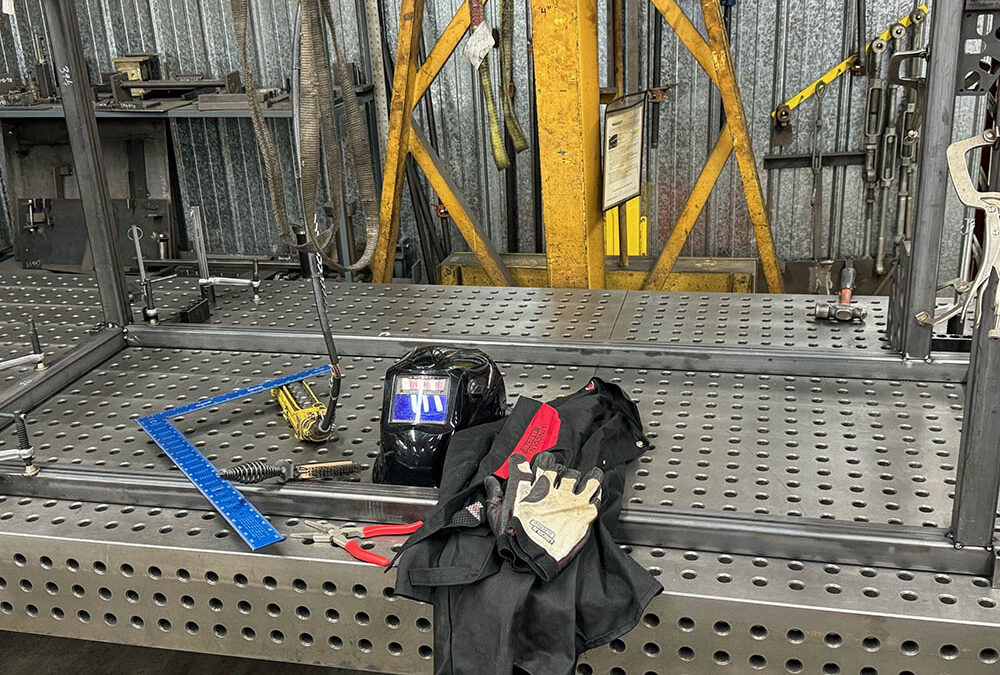
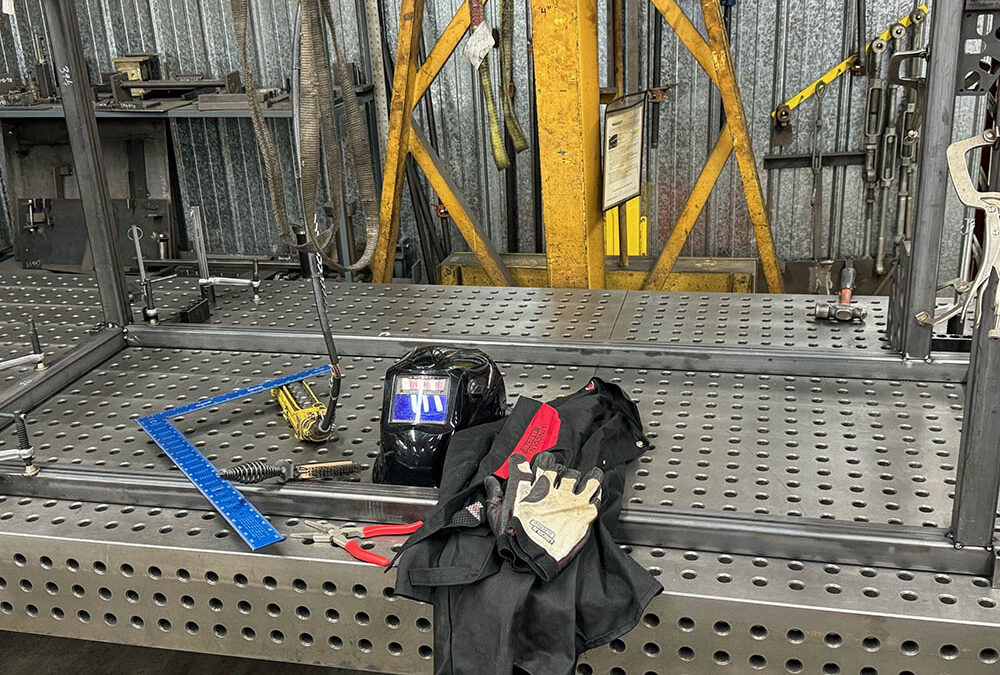
Welding Safety: How to Maintain Top Safety Standards
Mar 21, 2024 | Custom Welding Machinery, Robotic Welding Systems, Welding Systems
Image: Welding Personal Protective Equipment (PPE) Maintaining top safety standards in welding is not simply an expectation; it is imperative. Due to the risks inherent to welding processes, stringent safety measures must be implemented to protect operators and ensure...
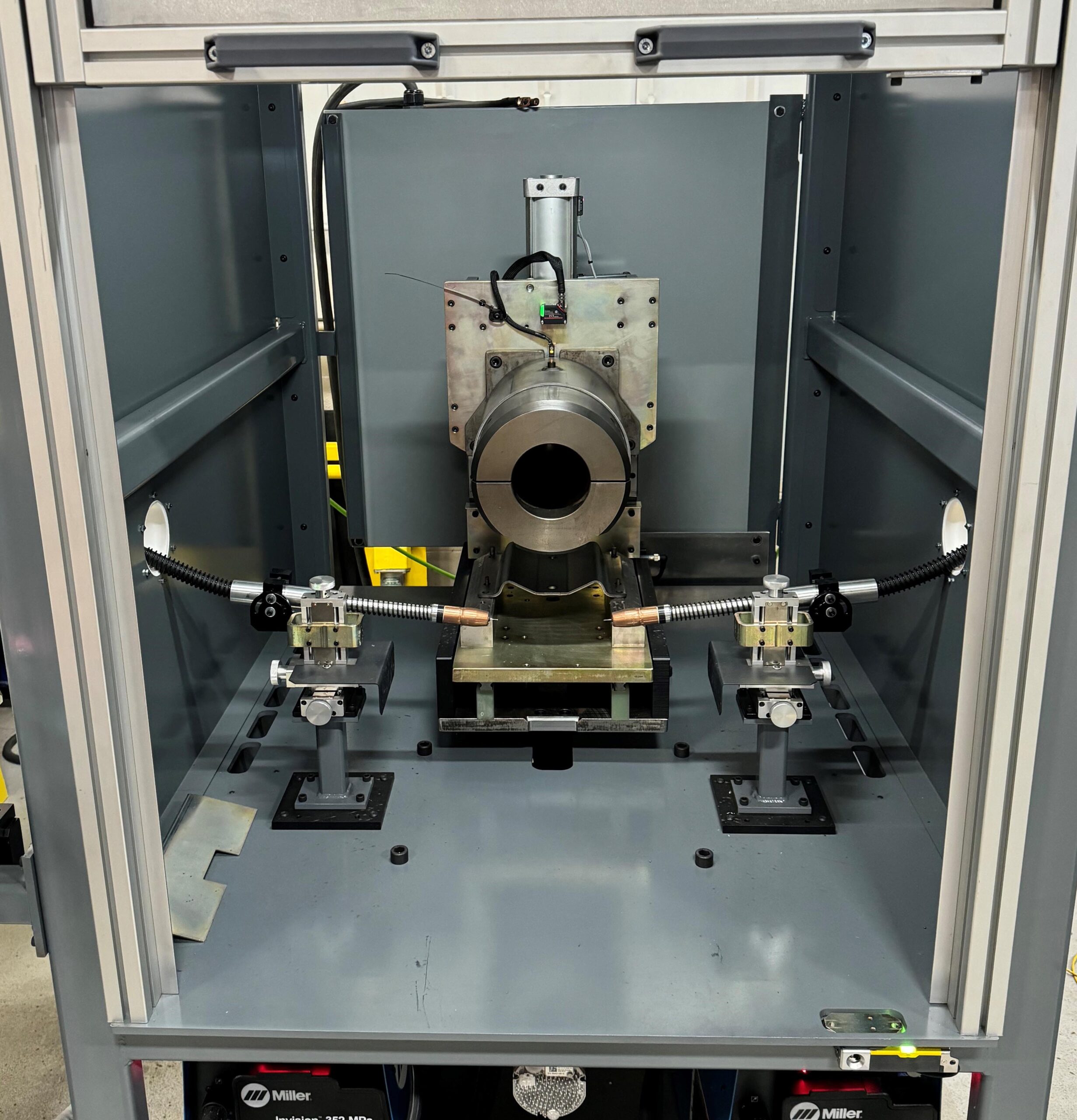
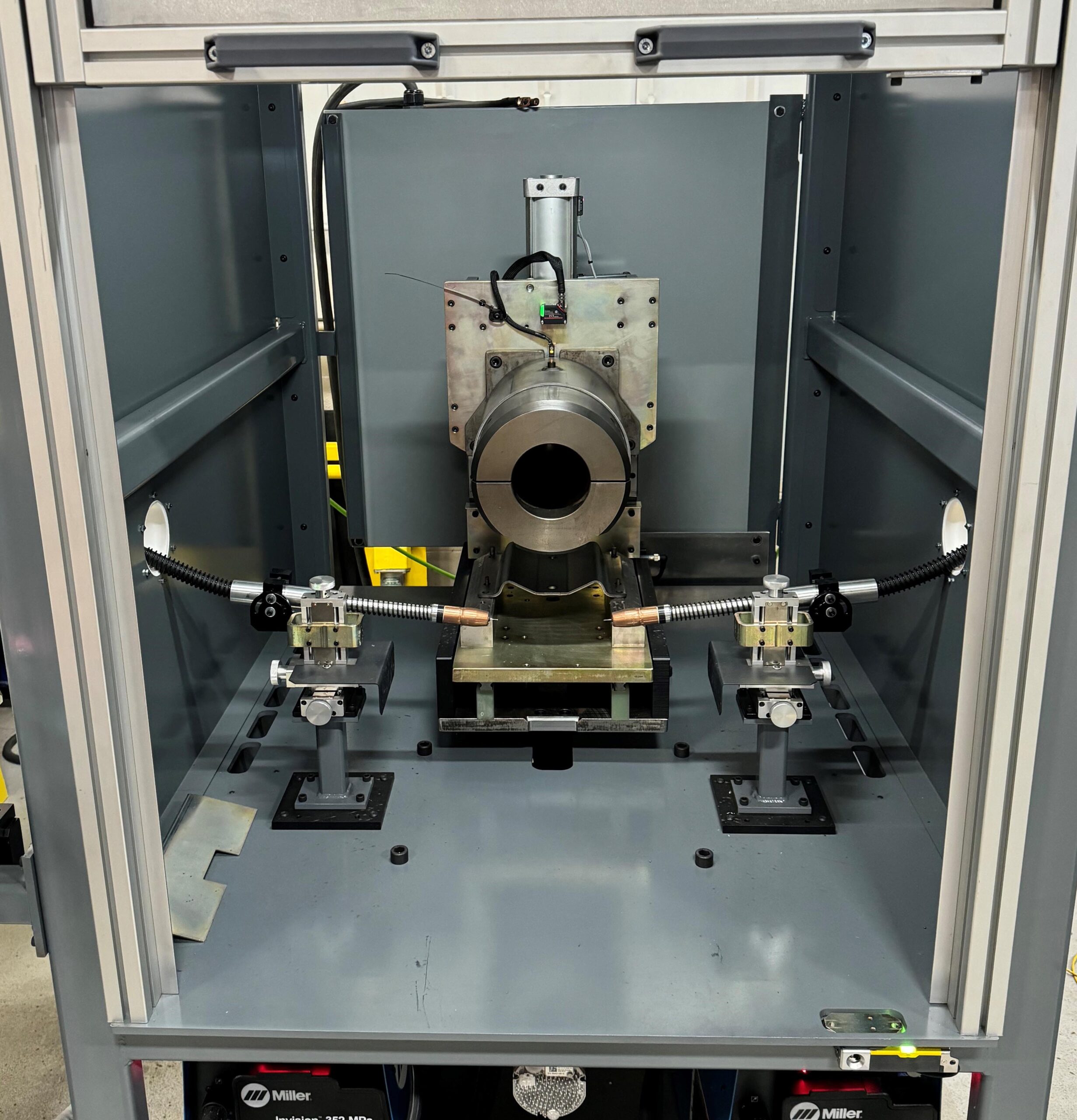
7 Factors to Consider for Picking the Best Welding Process
Jan 2, 2024 | Robotic Welding Systems, Semi-Automatic Welding Machine, Welding Systems
Selecting an ideal welding process is paramount to any welding project’s success, not only impacting weld quality but also productivity, cost efficiency and safety. In this post we will outline seven key factors you must keep in mind when identifying an optimal...
Search
Popular Posts
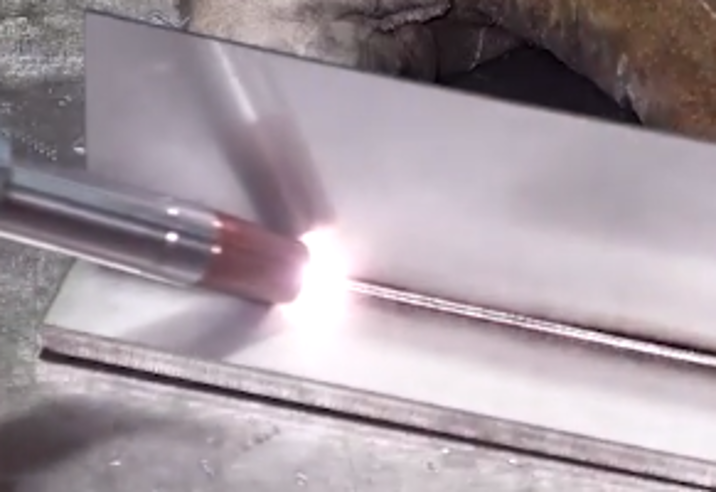
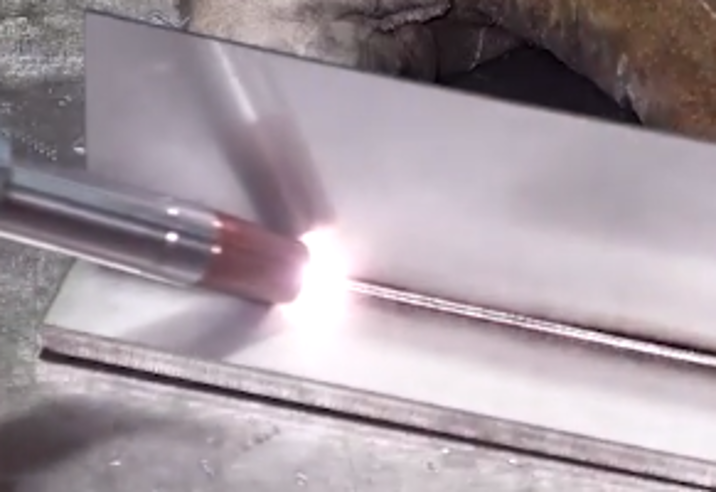
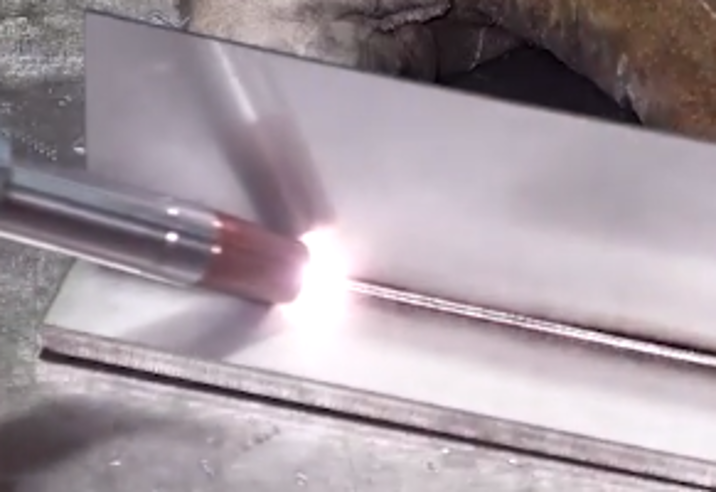
Exploring the Pros and Cons of Laser Beam Welding Technology
Apr 18, 2024
Bancroft Engineering stands at the forefront of manufacturing innovation, specializing in designing and producing cutting-edge automated welding equipment. Laser Beam Welding (LBW), a signature technology, is a testament to this. LBW uses laser beams to achieve...
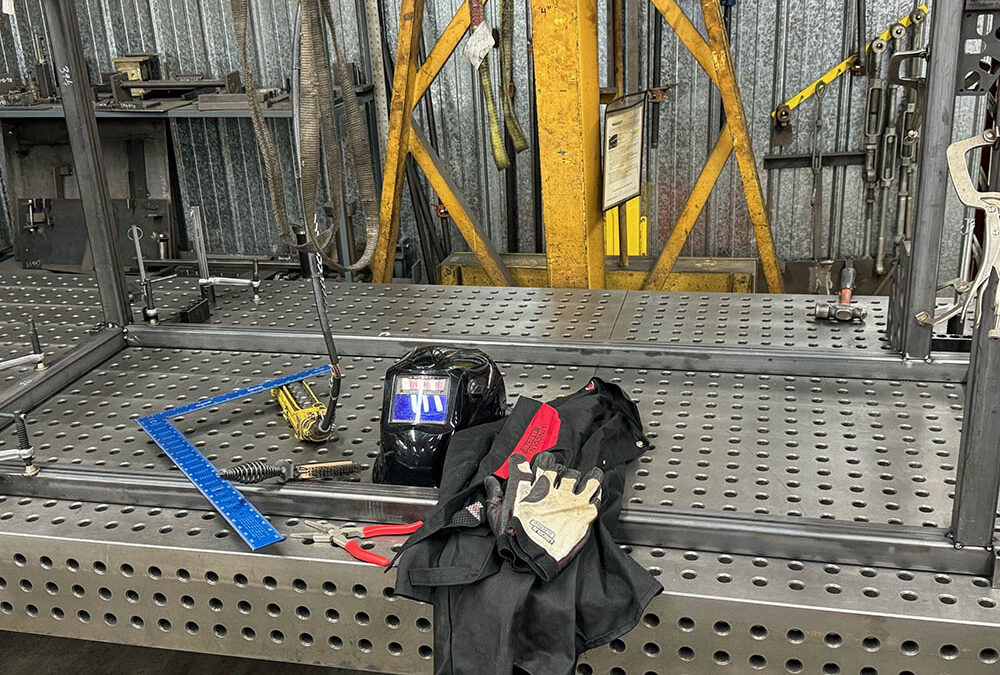
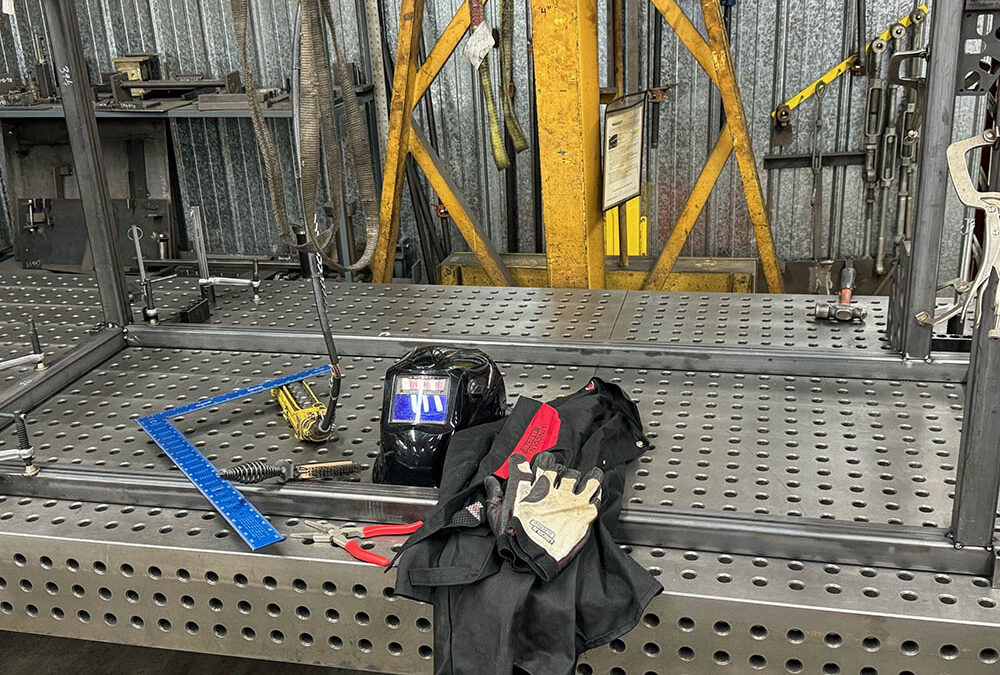
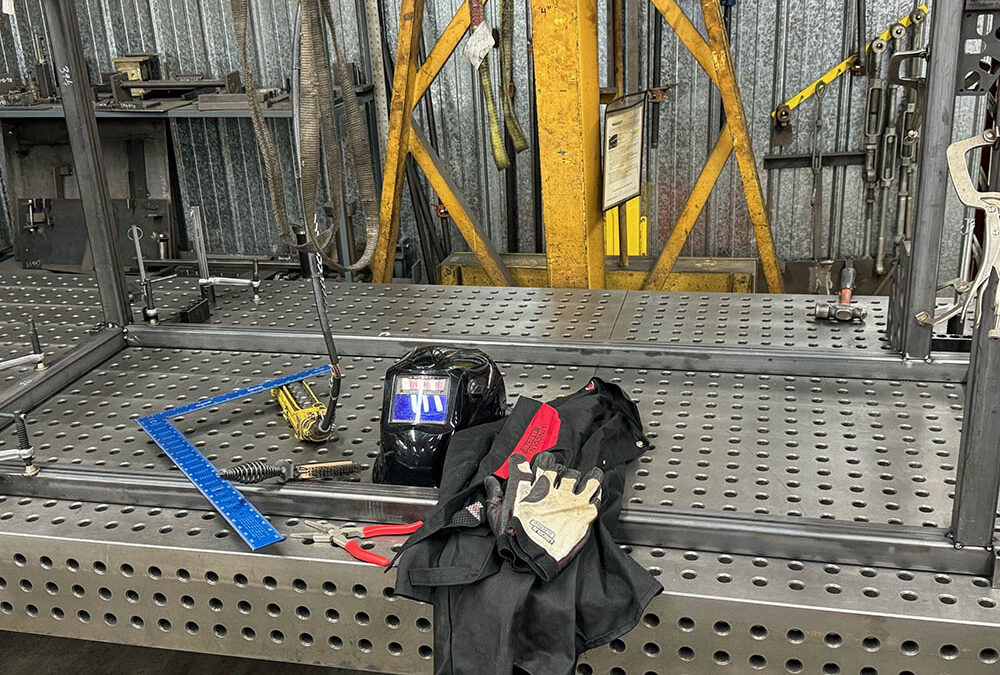
Welding Safety: How to Maintain Top Safety Standards
Mar 21, 2024
Image: Welding Personal Protective Equipment (PPE) Maintaining top safety standards in welding is not simply an expectation; it is imperative. Due to the risks inherent to welding processes, stringent safety measures must be implemented to protect operators and ensure...
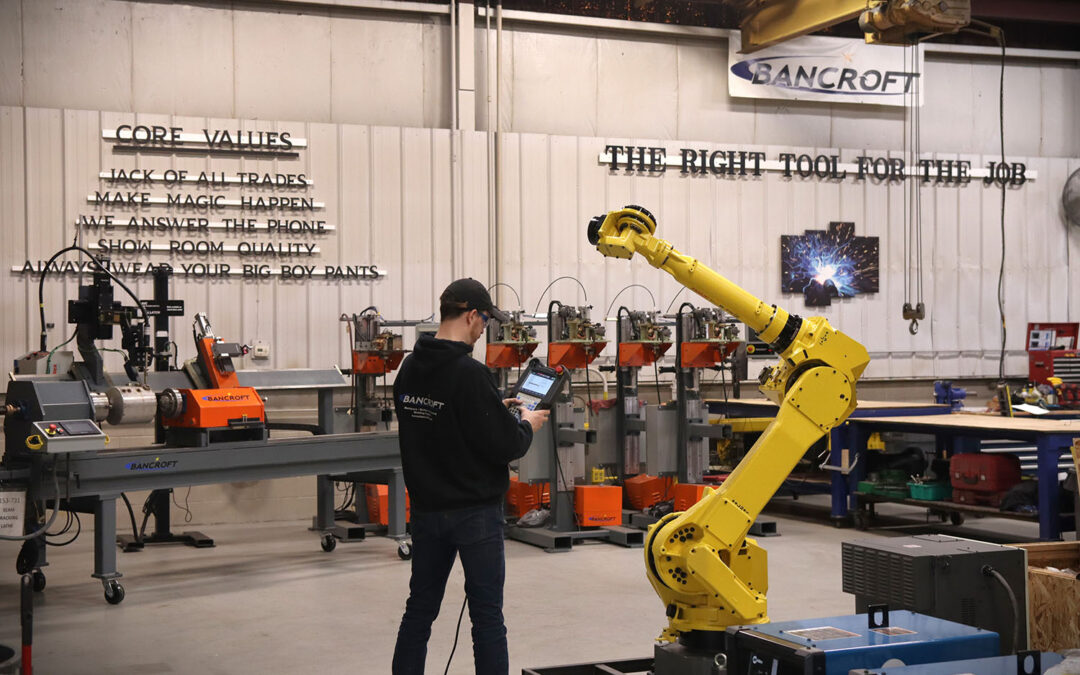
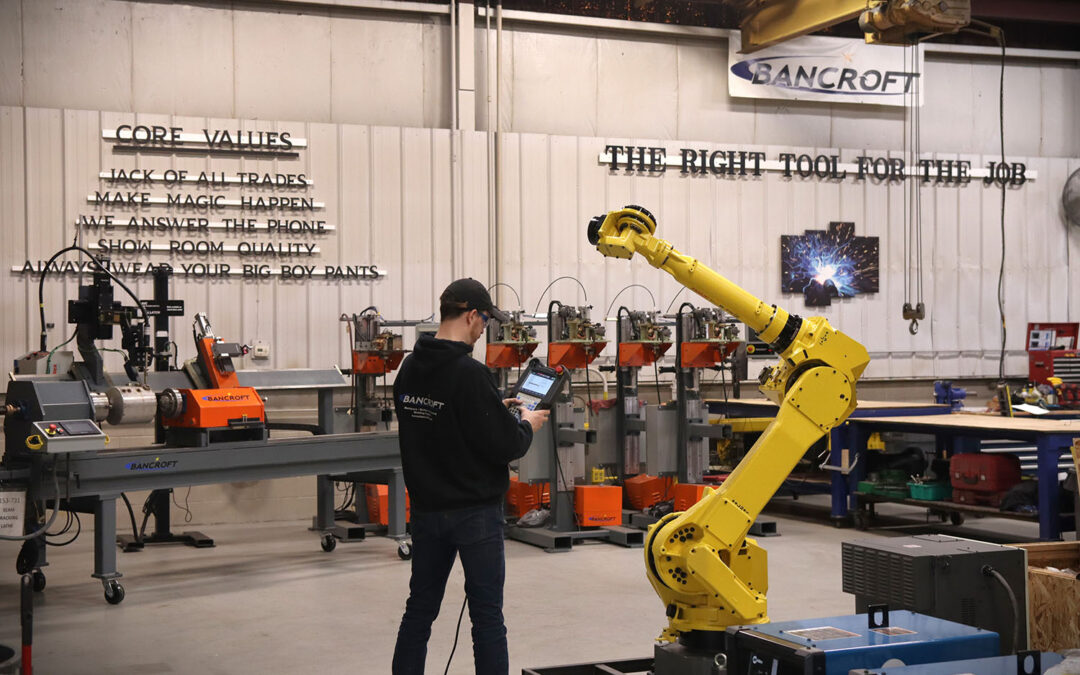
Debunking Myths: The Realities of Robotic Automation in Welding
Feb 8, 2024
Robotic automation has revolutionized industries from every angle, welding included. Yet despite its increasing prevalence and the myriad of advantages it brings, misconceptions remain as to what robotic welding automation can really do—particularly within precision...